Analog Devices Inc. and National Instruments Inc. have developed a MEMS test system based on PXI modules. ADI test executives, speaking at the NI Week users conference yesterday, said the system sharply reduces the cost of testing the MEMS microphones that ADI is making in high volumes for cell phone customers.
David Lammers, News Editor -- Semiconductor International, 8/5/2009
 |
Woody Beckford, ADI
|
Analog Devices Inc. (ADI, Norwood, Mass.) said it has sharply cut the cost of testing its high-volume MEMS microphones by using test equipment co-developed with National Instruments Inc. (NI, Austin, Texas). Based on the PC Extensions for Instrumentation (PXI) standard for modular instruments, the PXI test strategy could apply to a range of low-cost, high-volume MEMS and semiconductors, said Woody Beckford, a division fellow at ADI's test technology group.
In a keynote demonstration at the 2009 NI Week users conference going on this week in Austin, Beckford and Rob O'Reilly, director of business development for ADI's micromachined products division, said "big iron" testers don't meet cost objectives when the average selling price of a MEMS microphone, used in cell phones and other consumer products, is ~$1, with volumes of 2 million units per week.
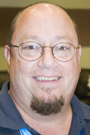 |
Rob O'Reilly, ADI
|
The large "big iron" ATE systems are designed for relatively high-pin-count devices, such as microprocessors, DRAMs and other high-performance ICs. The microphones used in many cell phones include a MEMS device that takes in acoustic signals and outputs a digital bit stream. It is packaged with a small ASIC, which includes an amplifier and an analog-to-digital converter. The two devices are put together in a tiny package that measures 2 x 3 x 1 mm.
For many MEMS devices, testing can account for as much as 40% of the total cost, an impractical amount for products that cost less than a dollar. "If we had stuck with Big Iron testers, that would have affected our margins," Beckford said.
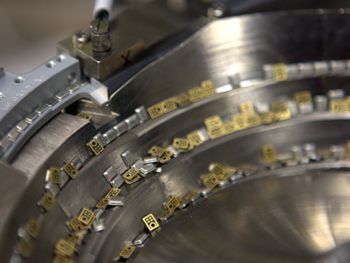 |
The MEMS microphone is packaged together with a small ASIC.
|
Large ATE systems take up a large footprint, draw relatively high amounts of power, and sell for several hundred thousand dollars, at minimum. Most of these test systems are optimized to test 512 memory chips in parallel, or multiple logic devices with a total of ~8000 digital pins. "Those systems are just not optimized for MEMS," Beckford said.
Scott Savage, a market development manager at NI's semiconductor test group, said thus far most PXI-based test systems have been used in characterization labs. However, NI has devoted resources to semiconductor test, introducing a more advanced source measurement instrument at NI Week capable of 10 pA resolution. The high-precision source measure unit (SMU) fits into a single 3U slot on a PXI chassis, and is capable of ±100 V outputs. The company introduced several other test-related products at NI Week.
"As PXI capabilities are continuously going up for semiconductor test, customers are working to drive down their test costs," Savage said.
Each PXI chassis holds about six test modules, depending on the configuration. O'Reilly said the 26 PXI chassis used by ADI currently to test the MEMS microphones can fit on a large industrial table, rather than the large room required in the case of conventional ATE tools. And since PXI systems plug into a standard 115 V power supply, the cost of the power is also much less.
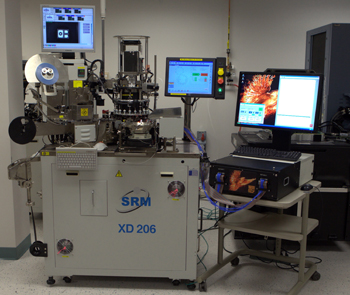 |
ADI and SRM worked to develop a vibration-free handler for the test system.
|
ADI worked with SRM Integration (Penang, Malaysia) to develop a custom handler for the MEMS microphones, which reduces noise and vibrations, Beckford said. The test time is only 700 msec, and the "relatively simple test requirements" support very high throughputs.
The PXI-based tester was developed in about nine months. Asked if similar PXI-based test systems will be able to reduce test costs for other semiconductors and MEMS, Beckford said, "Putting together a test system is a lot easier when everything is based on a PC. I don't see any drawbacks to it, and we can use an expanding suite of resources on the PXI standard. As consumer system chips become high-volume commodities and the process technology scales down to 65 nm and 45 nm and so on, built-in self-test becomes a lot more practical because we have more transistors to throw at the BIST macro. For MEMS also, there will be a lot more self-calibration on the device itself."
Savage said the PXI test modules are particularly effective for chips that have a relatively high amount of analog circuitry, including products such as digital-to-analog and analog-to-digital converters, wireless chipsets, power management ICs and amplifiers, as well as MEMS. About 60 different companies are developing PXI-based instruments now, with ~1500 different instruments on the market.
NI is emphasizing semiconductor test, according to CFO Alec Davern, speaking at a meeting with reporters at NI Week. "This downturn is going to be a game changer," he said. "During this time, true value gets exposed, and companies face a true test if they are adding value to their customers or not. That is why we see companies like ADI completely rethinking the cost of test."